In today’s rapidly evolving industrial landscape, the demand for efficiency and precision is greater than ever. One key technology that has emerged as a game-changer in various applications is the frequency drive (also known as a variable frequency drive, or VFD). This innovative device controls the speed and torque of electric motors by adjusting the frequency and voltage of the power supplied to them. As industries strive to enhance productivity while minimizing energy consumption, understanding the role and benefits of frequency drives becomes essential.
In this article, we will explore the fundamental principles behind frequency drives, their various applications, and the advantages they offer. Whether you’re an industry professional, a student, or simply curious about modern automation technology, this guide will provide you with valuable insights into how frequency drives can revolutionize motor control and energy management.
What is a Frequency Drive?
A frequency drive is an electronic device that regulates the speed and torque of electric motors by varying the frequency and voltage of the electrical supply. At its core, it consists of three main components:
- Rectifier: This component converts the incoming AC (alternating current) power into DC (direct current) power. The rectifier allows the frequency drive to manage the power supply more effectively.
- DC Bus: After rectification, the DC bus stores the DC power and smooths out fluctuations, ensuring a stable output. This is crucial for maintaining consistent motor performance.
- Inverter: The inverter converts the DC power back into AC power, adjusting the frequency and voltage according to the motor’s requirements. By controlling these parameters, the inverter enables precise speed and torque control.
How Frequency Drives Work
Frequency drives operate based on the principle of adjusting the frequency of the electrical supply. The speed of an AC motor is directly related to the frequency of the power supply. By increasing or decreasing the frequency, the drive can effectively speed up or slow down the motor.
For example, a standard motor operating at 60 Hz (Hertz) will run at its full speed. If the frequency is reduced to 30 Hz, the motor will operate at half speed. This flexibility allows for a wide range of applications, from simple fan control to complex robotic systems.
Applications of Frequency Drives
Frequency drives are widely used across various industries, including:
- HVAC Systems: They regulate the speed of fans and pumps, enhancing energy efficiency and comfort in commercial and residential buildings.
- Manufacturing: In production lines, frequency drives control conveyors, mixers, and other machinery to optimize processes and reduce waste.
- Water and Wastewater Treatment: They manage the operation of pumps, ensuring efficient water distribution and treatment processes.
- Mining and Mineral Processing: Frequency drives are utilized in crushers, mills, and other equipment, improving operational efficiency and safety.
Advantages of Frequency Drives
Implementing frequency drives offers numerous benefits, such as:
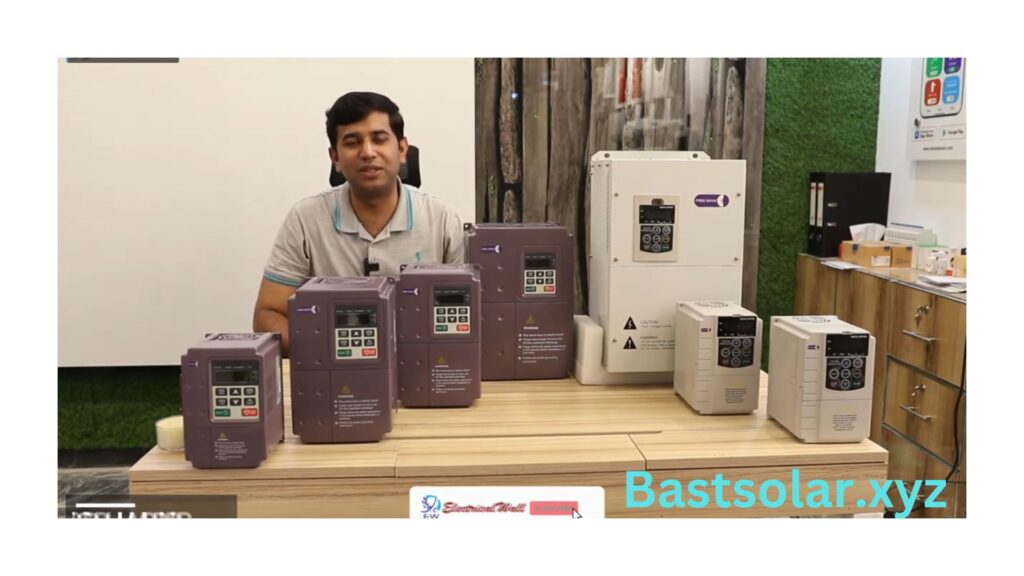
- Energy Savings: By matching motor speed to the load requirement, frequency drives can significantly reduce energy consumption, leading to lower operating costs.
- Improved Process Control: Precise speed and torque control allow for better management of industrial processes, enhancing product quality and consistency.
- Reduced Wear and Tear: Soft starts and stops minimize mechanical stress on equipment, extending the lifespan of motors and reducing maintenance costs.
- Enhanced System Reliability: Frequency drives can provide fault protection and diagnostics, improving the overall reliability of motor-driven systems.
Conclusion
In summary, frequency drives play a pivotal role in modern motor control systems, enabling industries to achieve greater efficiency, reliability, and flexibility. By adjusting the frequency and voltage supplied to electric motors, these devices provide precise control over speed and torque, which is essential for optimizing various processes across multiple sectors.
The advantages of frequency drives—such as energy savings, improved process control, reduced mechanical stress, and enhanced system reliability—underscore their importance in today’s industrial landscape. As businesses continue to focus on sustainability and cost-effectiveness, the adoption of frequency drives will likely expand, driving innovation and efficiency in operations.
References
To support the insights and information presented in this article about frequency drives, here are some valuable references and resources:
- Books and Articles:
- “Electric Motor Drives: Fundamentals, Technologies, and Applications” by R. Krishnan. This book provides comprehensive coverage of the principles and applications of electric motor drives, including frequency drives.
- “Variable Frequency Drives: Principles of Operation” by V. P. P. Rao. A detailed guide on the operation and application of variable frequency drives in various industrial settings.
- Industry Resources:
- IEEE Xplore: A digital library that offers access to technical literature in electrical engineering, including studies and papers on frequency drives and their applications.
- The Association for Electrical Equipment and Technology (NEMA): Provides guidelines and standards related to electric motors and drives, including energy efficiency standards.
- Websites and Online Courses:
- National Instruments: Offers articles and tutorials on frequency drives and control systems, ideal for both beginners and experienced professionals.
- Coursera: Hosts various online courses related to industrial automation and control systems, which include modules on frequency drives.
- Manufacturer Documentation:
- Many manufacturers, such as Siemens, Schneider Electric, and Allen-Bradley, provide extensive documentation, case studies, and application notes on their frequency drive products, which can be valuable for practical insights and specifications.
By consulting these resources, readers can deepen their understanding of frequency drives and their significance in modern industrial applications. This knowledge not only enhances technical expertise but also aids in making informed decisions regarding the implementation and management of these critical technologies.
FAQs about Frequency Drives
1. What is a frequency drive?
A frequency drive, also known as a variable frequency drive (VFD), is an electronic device that controls the speed and torque of an electric motor by adjusting the frequency and voltage of the power supplied to it.
2. How does a frequency drive work?
Frequency drives operate by converting incoming AC power into DC power through a rectifier, storing it in a DC bus, and then converting it back to AC power using an inverter. By varying the frequency of the AC power, the drive can adjust the speed of the motor.
3. What are the benefits of using a frequency drive?
The main benefits include energy savings, improved process control, reduced mechanical stress on equipment, and enhanced system reliability. They enable precise control of motor speed and torque, leading to more efficient operations.
4. In what applications are frequency drives commonly used?
Frequency drives are widely used in HVAC systems, manufacturing processes, water and wastewater treatment, mining, and many other industries where precise motor control is required.
5. Can frequency drives be retrofitted into existing systems?
Yes, frequency drives can often be integrated into existing systems to enhance efficiency and control. However, it’s essential to consider compatibility with existing equipment and specific application requirements.
6. Are there any downsides to using frequency drives?
While frequency drives offer many advantages, they can introduce harmonic distortion into the electrical system, which may require additional filtering solutions. Additionally, they may have a higher initial cost compared to traditional motor control methods.